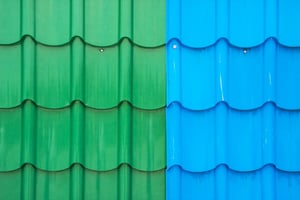
Composites, Ceramics & Glass Industry
ADVANCED MIXING SOLUTIONS FOR THE COMPOSITES, CERAMICS & GLASS INDUSTRY
The composites, ceramics, and glass industry is a diverse and innovative sector that plays a crucial role in various applications, from aerospace and automotive to construction and consumer goods. This industry involves the production of advanced materials that offer superior strength, durability, and performance compared to traditional materials. Composites, ceramics, and glass are essential for creating lightweight, high-strength components, insulating materials, and aesthetically pleasing products. The demand for these materials continues to grow as industries seek to improve efficiency, reduce weight, and enhance the overall performance of their products.
One of the significant challenges in the composites, ceramics, and glass industry is achieving precise and consistent mixing of raw materials and additives. This is essential to ensure the quality, uniformity, and performance of the final products. Admix addresses these challenges by providing advanced mixing solutions specifically designed for this industry. Our high-shear mixers and agitators are capable of handling a wide range of viscosities and particle sizes, ensuring thorough dispersion and homogenization of materials. This results in superior product quality, whether it's a composite material, ceramic component, or glass product.
Admix's equipment is also known for its reliability and efficiency, which are critical factors in the composites, ceramics, and glass industry. Our mixers are engineered to minimize downtime and maintenance, allowing for continuous and efficient production processes. Additionally, our mixing technology is designed with energy efficiency in mind, helping to reduce operational costs and environmental impact. By leveraging Admix's advanced mixing solutions, companies in the composites, ceramics, and glass industry can achieve higher productivity, improved product quality, and a more sustainable production process.
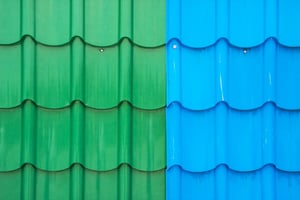
Mixing/Processing Problems Solved
- Poor dispersion of active ingredients
- Fillers resulting in inconsistent shelf life
- Need for excessive remixing at point of use
- Curing problems
- Lumps
- Plugging of applicator equipment
- Difficulty adding viscosity and rheology modifiers
- Long milling/secondary particle reduction process
- Long blend/dissolving times
Composites, Ceramics & Glass Industry Solutions
-
All
-
High Shear
-
In-tank
-
Inline
-
Dispersion
-
Diaf
-
Lab Mixers
-
Powder Induction
-
Low Shear
-
In-Tank
-
Accessories
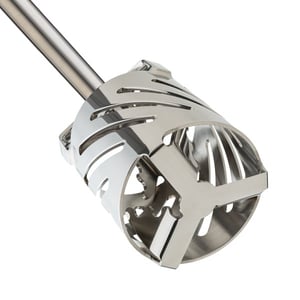
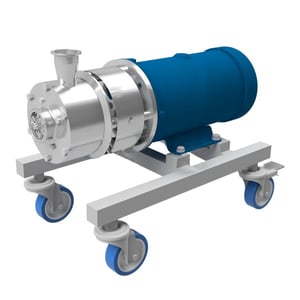
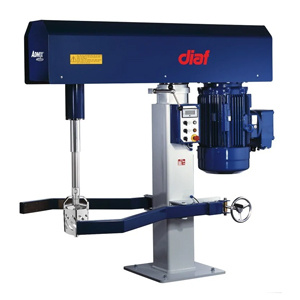
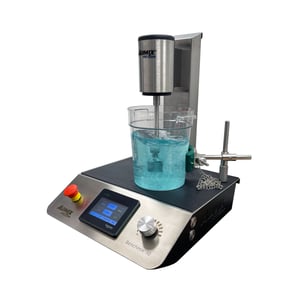
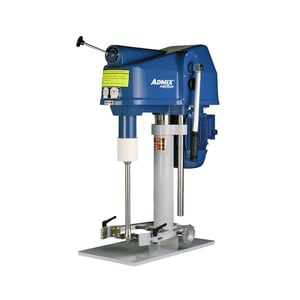
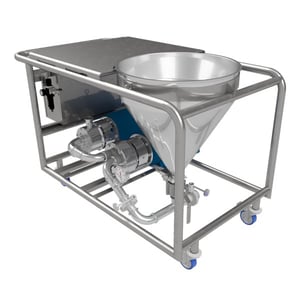
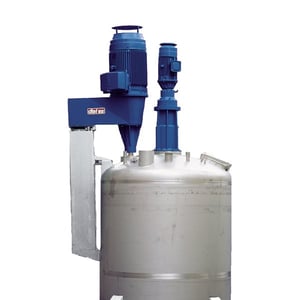
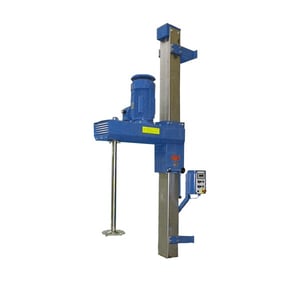
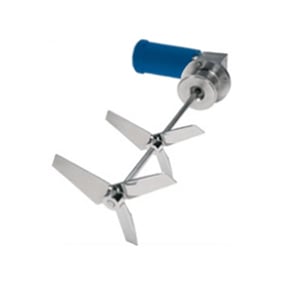
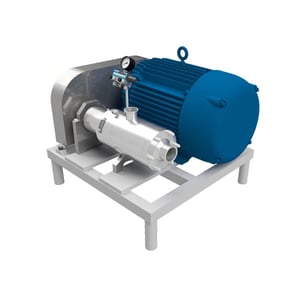
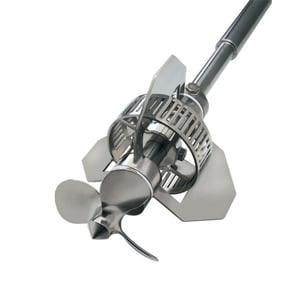
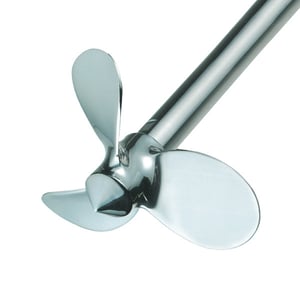
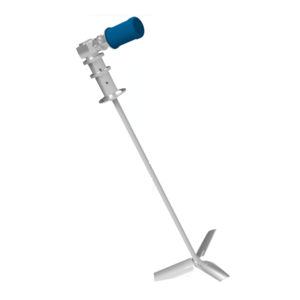
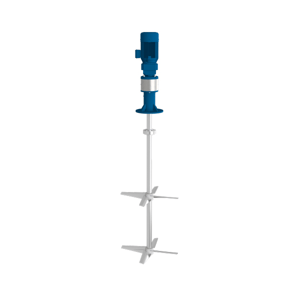

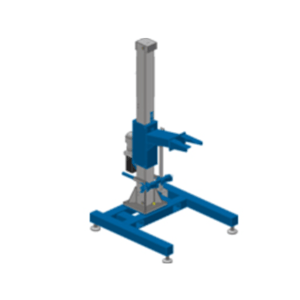
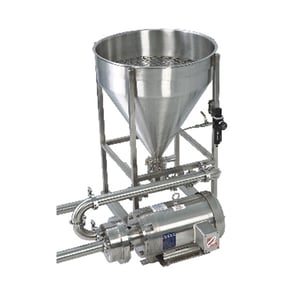
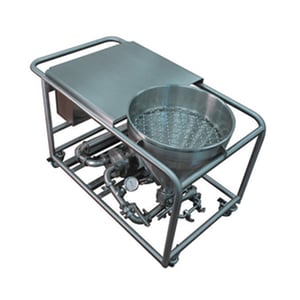
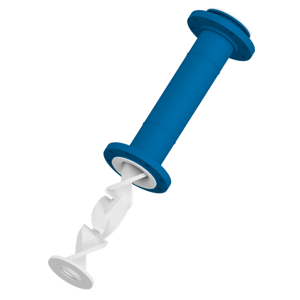