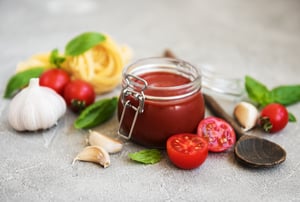
The Tomato Industry
ADVANCED TOMATO BLENDING & PROCESSING SOLUTIONS
Admix hygienic mixers have become a cornerstone in the world of tomato processing, with a global footprint spanning hundreds of installations. Our mission is to empower you in the art of tomato paste enhancement, pomace reutilization, viscosity amplification, and the elevation of product finish and brilliance. Through our innovative tomato processing solutions, we've enabled a multitude of clients to unlock the full potential of their tomato processing endeavors, facilitating the creation of superior paste, standardization processes, and the rejuvenation of paste for the improved formulation of ketchup, tomato sauces, soups, salsa, and a variety of tomato-centric delights.
If you manufacture these products, we can help improve your process:
- Tomato paste/concentrate
- Tomato juice
- Ketchup
- Tomato, pizza, marinara, or barbecue sauce
- Chili, soups, or salsa
- Vegetable juice
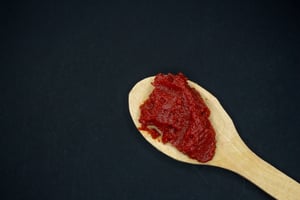
Mixing/Processing Problems Solved
Our technical knowledge, field experience, and innovative products provide several benefits to processing these tomato-based products including:
- Thicker, more viscous paste with improved Bostwick and increased yield- Consistent standardized paste through either batch or inline blending
- Ultra rich ketchup with no syneresis
- Thick or thin tomato or pizza sauce
- Superior chunky or milled salsas
- Smooth soups
Rotosolver high shear mixer
If your production line requires 100% wetting out of powders, and an easy-to-clean design that meets 3-A sanitary requirements, the Rotosolver® is the solution. The Rotosolver design includes two additional shear zones providing higher overall shear rates, improved dispersion, and reduced energy consumption for volumes up to 10,000 gallons (37,854 liters).The Rotosolver outperforms competitors in key performance areas. For various applications, it has delivered up to:
- 50% less energy consumption
- 600% higher flow rates
- 20% higher tip speeds
- 6 times more throughput than conventional mixers
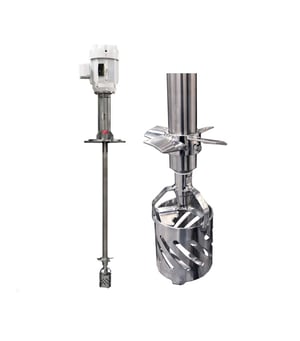
Dynashear inline high speed emulsifier
The Dynashear® inline high speed emulsifier disperses gums, stabilizers, proteins and sweeteners in a single pass delivering batch times as low as 3-5 minutes and less air entrainment. With flow rates up to 175 GPM, the 3-A compliant Dynashear delivers smooth product every time with no fisheyes or agglomerates. The two-stage rotor/stator action allows processors to run longer and CIP less frequently. When installed upstream of inline strainers or HTST balance tanks, the Dynashear improves your process, preventing clogged strainers and extending the life of pumps, valves, and seals.
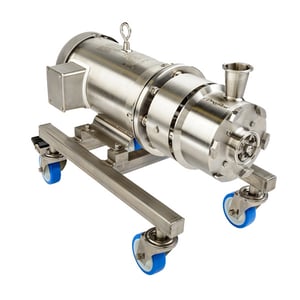
Fastfeed powder induction system
Discover the revolution in ingredient processing with the Fastfeed® powder induction and dispersion system. This cutting-edge system effortlessly integrates, moistens, and disperses a variety of ingredients, completely eradicating any lumps. Whether it's proteins, gums, starches, vitamins, fiber, sweeteners, stabilizers, emulsifiers, flavors, or colors, our system handles them with unparalleled efficiency, dispersing up to 450 pounds (204 kilograms) per minute seamlessly in a single pass. Not only does it outperform traditional tank mixers by consuming up to 70% less energy, but it also guarantees consistency batch after batch by introducing powders at a consistent rate every time. Further enhancing its value, the Fastfeed system significantly reduces batch times and minimizes air entrainment, offering a smooth, streamlined process. Additionally, it addresses workplace safety and cleanliness by eliminating the dust associated with dumping powders into open tanks and enhances operator safety by allowing powders to be added from the safety of floor level.
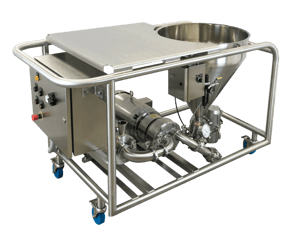
Boston Shearmill wet mill/homogenizer
The 3-A compliant Boston Shearmill® wet mill/homogenizer outperforms conventional shear pumps and colloid mills and provides very high throughputs at extreme shear rates. Inline rotor-stator machines deliver 24/7 operation; reduce solids particles with minimal dust formation; and withstand uneven flow patterns, jolts, and pressure fluctuations. And for milling of soft particles to <1 micron, or hard particles down to 1-2 microns, the shearmill produces superior particle size reduction, often in a single pass at high production rates.
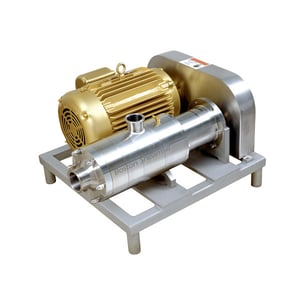