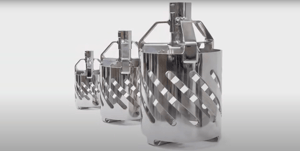
ROTOSOLVER CX
OVERVIEW
- High-intensity optimum shear
- 100% dissolving, hydrating or suspension
- From lab models to production sizes up to 100 HP
- Mixing head diameter sizes, motors, seals, mountings, and more
- Single shaft, obstruction-free design
- One-piece clean-in-place (CIP) mix head
- Optional secondary impellers
Rotosolver® CX vs. the competition
Not all high shear mixers are created equal. When going head-to-head with the competition, the Admix Rotosolver comes out on top across many key performance areas.
Rotosolver CX
Competition
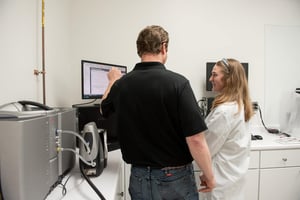
HOW IT WORKS
The unique design of the Rotosolver CX produces high flow, in addition to high shear, resulting in batch process times that are much faster than conventional in-tank rotor/stator designs.The Rotosolver CX mix head design generates four stages of mixing action for optimal for dispersion of chemicals:
- Product flow is drawn into the mixing head from above and below. The resultant flow creates vigorous tank motion, pulling materials and powders from the top of the tank surface (typically the toughest to disperse), instantaneously exposing them to shear zones in the Rotosolver CX shear head, where these materials are mechanically ripped apart (dispersed).
- The two high-velocity, counter-current streams converge within the shear head, creating high turbulence and hydrodynamic shear.
- Pressure, created by the two streams, forces material out the side slots of the shear head, where the resulting radial streams are subjected to further mechanical shear, as material passes through the edges of the slots in the chamber wall.
- The high velocity radially discharged streams impact the slower moving tank flow for additional hydrodynamic shear and circulation, thus ensuring high flow, with no dead spots in the mix tank.
TRY BEFORE YOU BUY
Our trial program offers a hands-on opportunity to test our state-of-the-art equipment, ensuring it meets your standards for quality and performance. Take advantage of this risk-free option to see firsthand how our solutions can benefit your business operations.
Rotosolver CX Options
HEAD SIZES
Sizes range from 29 mm – 300 mm diameter.
Note: 29 mm and 40 mm heads are for the Benchmix lab scale mixer only.
MOTORS
- High Efficiency TEFC or TEXP
- White Washdown Duty
- Painted
SEALS
- Low Pressure Lip Seal
- Double, Liquid-Barrier Mechanical Seal
- Double, Gas-Charged Mechanical Seal
MOUNTING
- Standard Flange (open tank)
- 316SS C-clamp (small size only)
- Clamp / Ferrule
- Hydraulic White Epoxy Mobile or Wall Lift Stand
MORE
- Low Profile Belt Drive for Low Headroom Application
- Detachable Shafts
RELATED RESOURCES
Filter by type.
-
All
-
Datasheet
-
Video
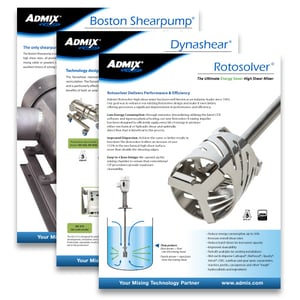
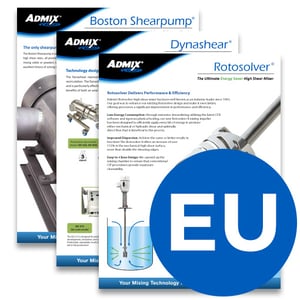
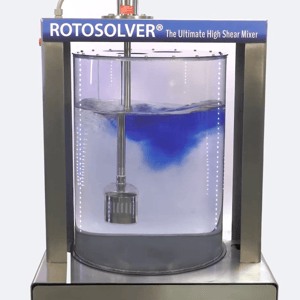
Watch our patented Rotosolver in action and see how it can improve your process.
Read More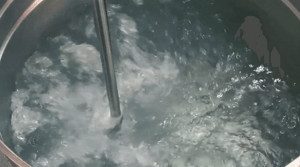
Achieving a homogeneous fluid product— consistent in physical makeup— is crucial. Two primary mixing approaches come into play: high shear and low shear mixing.
Watch NowRELATED BLOG POSTS
Ingredient Spotlight: Pigment
Why Proper Dispersion Matters in Chemical Mixing
Optimizing Manufacturing with Diamix CX Mixing Technology
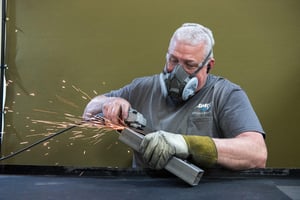