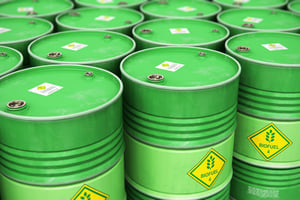
Biofuel & Petroleum Industry
INNOVATIVE MIXING SOLUTIONS FOR THE BIOFUEL & PETROLEUM INDUSTRY
The biofuel and petroleum industry is a cornerstone of the global energy sector, providing essential fuels for transportation, heating, and industrial processes. This industry is characterized by its complexity and the need for precise and efficient processing techniques to convert raw materials into usable fuels. With the increasing demand for sustainable energy sources, biofuels have gained significant attention as an alternative to traditional petroleum-based fuels. Biofuels, derived from renewable resources such as plant biomass, algae, and waste materials, offer a promising solution to reduce greenhouse gas emissions and dependence on fossil fuels.
One of the critical challenges in the biofuel and petroleum industry is achieving efficient and consistent mixing of various raw materials and additives. This is where Admix comes into play, offering advanced mixing solutions tailored to the unique needs of this industry. Our equipment is designed to handle the rigorous demands of biofuel and petroleum processing, ensuring optimal blending and homogenization of materials. Our high-shear mixers and agitators are capable of processing a wide range of viscosities and densities, from light biofuels to heavy crude oils, ensuring a uniform and stable mixture.
Admix’s innovative mixing technology not only enhances the quality and consistency of the final product but also improves production efficiency and reduces operational costs. Our equipment is engineered for durability and reliability, minimizing downtime and maintenance requirements. Additionally, Admix mixers are designed with energy efficiency in mind, helping to reduce the overall environmental impact of the production process. By leveraging our advanced mixing solutions, companies in the biofuel and petroleum industry can achieve superior product quality, increased efficiency, and a more sustainable production process.
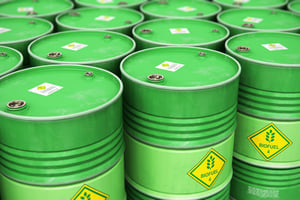
Mixing/Processing Problems Solved
- Poor dispersion of active ingredients and fillers- Inconsistent shelf life/need for excessive remixing at point of use
- Curing problems
- Lumps
- Plugging of applicator equipment
- Difficulty adding viscosity and rheology modifiers
- Long milling/secondary particle reduction process
- Difficulty achieving consistent results on emulsions
- Difficulty in preparing/adding viscosity modifiers
- Difficult to blend/dissolve concentrated surfactants
Biofuel & Petro Industry Solutions
-
All
-
High Shear
-
In-tank
-
Inline
-
Dispersion
-
Diaf
-
Lab Mixers
-
Powder Induction
-
Low Shear
-
In-Tank
-
Accessories
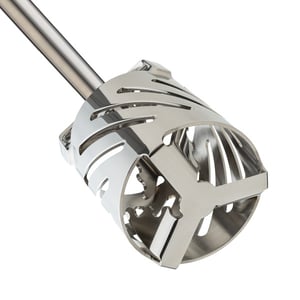
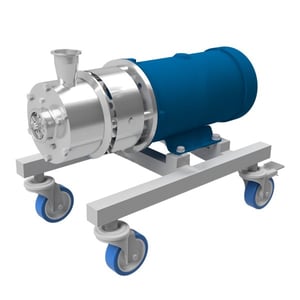
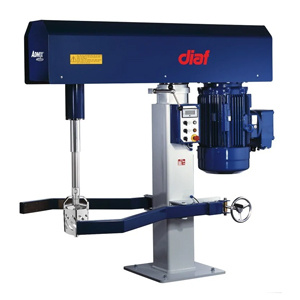

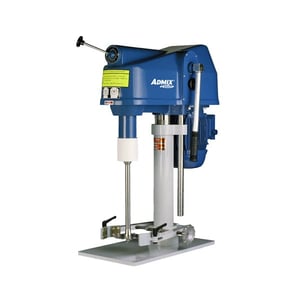
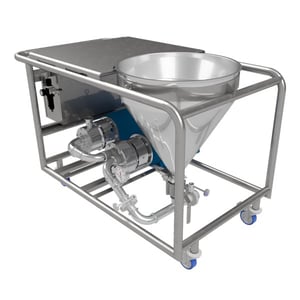
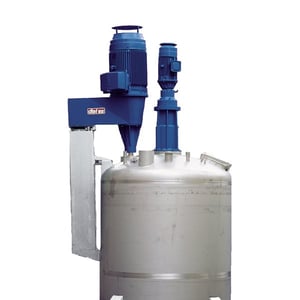
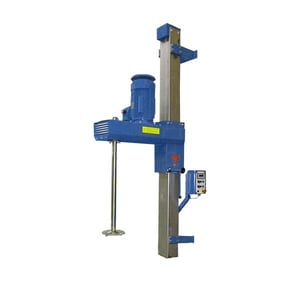
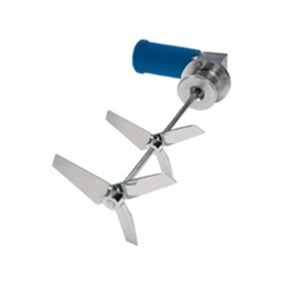
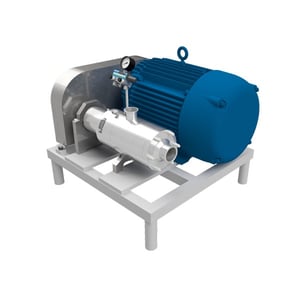
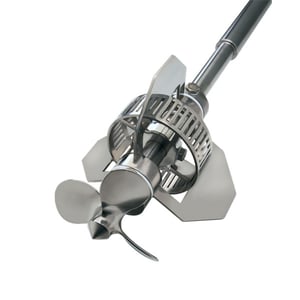
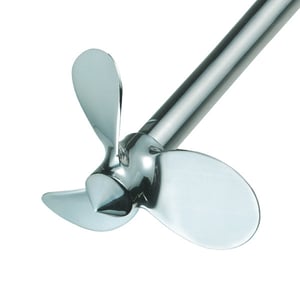
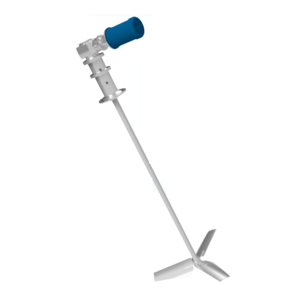
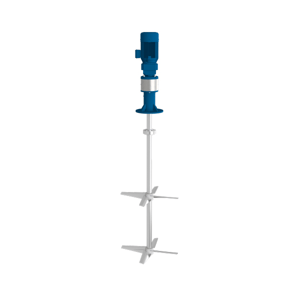
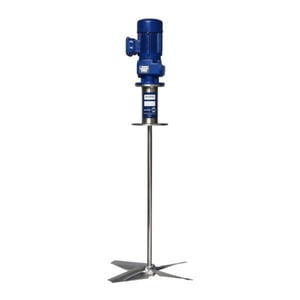
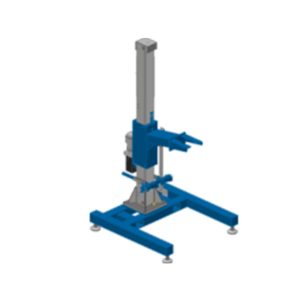
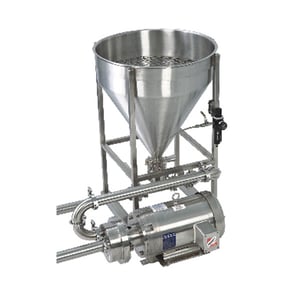
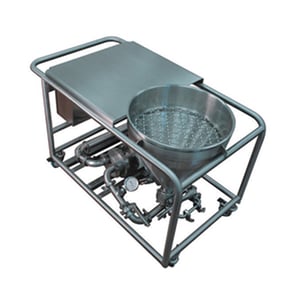
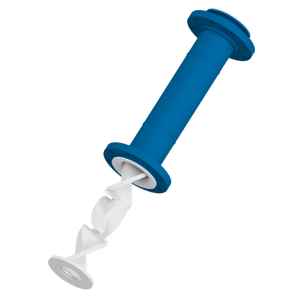