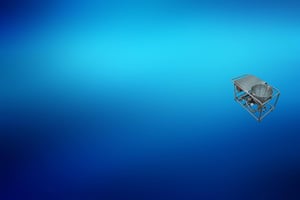
PIC
OVERVIEW
Leveraging the innovative venturi principle for unparalleled suction of both dry and liquid materials, our PIC system is designed with user experience in mind, featuring an ergonomic, waist-high hopper that simplifies the addition of ingredients into the mix. Capable of processing an impressive 50-200 pounds per minute, the system's efficiency is adaptable based on your specific settings and operational conditions. This flexibility ensures that we support your needs reliably, enhancing your process efficiency with thoughtful, innovative solutions.
Key Features:
- Reduced operator injury
- Reduced accidents
- Fast ingredient addition
- Reduced mix times
- Improved yields
HOW IT WORKS
The PIC™ System includes an ergonomic table and washdown control panel with a high performance powder suction pump that vacuum conveys from 3 to over 200 pounds per minute of any powder or solid.
For materials that are easily dissolved or suspended, the system discharge could then be sent on to the next step in the process. If materials require shear to properly disperse, deagglomerate or emulsify, they can be recirculated through a batch tank with in-tank high shear mixer. Alternately, the material can be processed through a Dynashear or Boston Shearmill for in-line high shear mixing, without the need for a batch mixer.
Basic Rules for Use
- Maximum viscosity before or after ingredient introduction is 2500 cps.
- Maximum allowable head on discharge side is 10 psi. If head loss exceeds recommended levels, a booster pump on the discharge piping should be installed.
- Minimum incoming flow rate for the system is 35 GPM.
If soy protein, carrageenan, starch or similar products are used, a Fastfeed system may be necessary.
One significant point for all users of powder induction equipment to be aware of: It is very difficult to control with absolute precision the volume of the entrained material and its instantaneous ratio to the motive liquid. Most often, powder induction systems are mounted in a batch mixing process to insure the desired recipes are achieved.
Model Specifications
Scroll to the right if needed to view all information.
* Higher viscosities achievable with the addition of a positive displacement take-away pump
PIC Options
- Electropolished hopper and wetted parts
- Special hopper design for difficult powders, to include air sparge, water flush, and vibration systems
- Alternate pipe fittings available
- Various motor types for pump drive
- Special elastomers
- Actuated valves
RELATED BLOG POSTS
No Ladders, No Clumps, No Problem: Fruit Winery Simplifies Batch Processing with the Admix PIC-100
How One Inline High Shear Mixer Became the Go-To Solution for Sauces, Soups, and More
Ingredient Spotlight: Starches
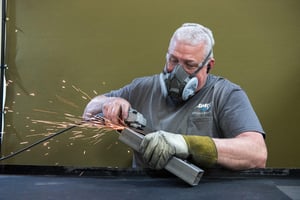