Recently I was at a customer plant for an installation of a large Rotosolver®. This high shear mixer was about 16 feet tall with a 225mm diameter mixing head.
The customer makes fine chemicals for agrochemicals, pharmaceuticals, adhesives, coatings, and other products. This was an interesting installation because it was a customized solution. They needed to run the Rotosolver at 1800RPM which was a very high speed for the mixer size. The concern was that the added speed would result in increased bearing temperatures that could cause premature wear on the bearings, and eventual failure.
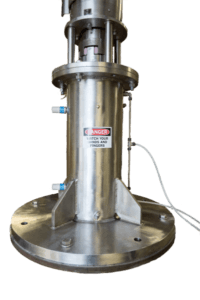
To accommodate the customer’s need to run at very high speeds without causing premature wear, we customized the mixer with cooling sleeves that were added to the upper and lower bearing bores in the bearing frame. This enabled for cold water to be run through the bearing frame and around the outside of the bearings, keeping bearing temperatures low. The chemicals producer reported that the “dual bearing cooling is very effective.”
We further customized the mixer with Machine Condition Indicators installed on the exterior of the bearing frame at the bearing positions. Without the MCIs operators would have to climb up high to a platform that is difficult to access. The MCIs are essentially a check engine light for the mixer. They measure temperature and vibration and will show green LEDs to indicate they are within the normal range. If the sensor measures excess heat or vibration, it will show red LEDs. This provides a simple solution for a quick visual inspection of the unit to confirm it is running well.
Admix is happy to work with you to provide customized solutions for your needs. Contact us to improve your process, maintenance reliability or other mixing situation you are experiencing. We have the engineering, manufacturing, and mixing expertise to work with you and provide a beneficial solution.