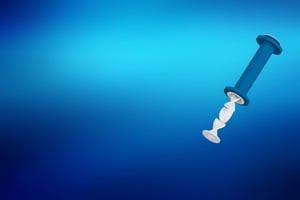
ADMIXER CX
OVERVIEW
The Admixer CX even stirring characteristics of this low shear static mixer are ideal for many jobs.
At the heart of a static mixer lies an elegantly simple concept: as fluid journeys through a pipeline, it encounters a carefully designed geometric array of mixing elements. This innovative arrangement within the mixer’s core ingeniously directs the flow to split, blend, then split and blend again in a seamless dance until the mixture reaches perfection. This process not only exemplifies our commitment to providing solutions that enhance efficiency and precision but also reflects our dedication to supporting our clients' needs with reliable and thoughtful engineering.
The flow then continues in a pipe as if it had gone through conventional batch mixing in tanks, with the distinct difference that the degree of homogeneity can be precisely controlled within the sanitary static blender.
- Highly predictable mixing and dispersion
- 100% product uniformity and distribution from controlled shear and turbulence
- Mechanical reliability with no moving parts, no electrical requirements, easy installation
- Low capital cost and maintenance
- 50-90% less power consumption than mechanical mixers
- Superior corrosion or abrasion resistance
- Excellent process versatility – capable of handling viscosities over 1 million cps
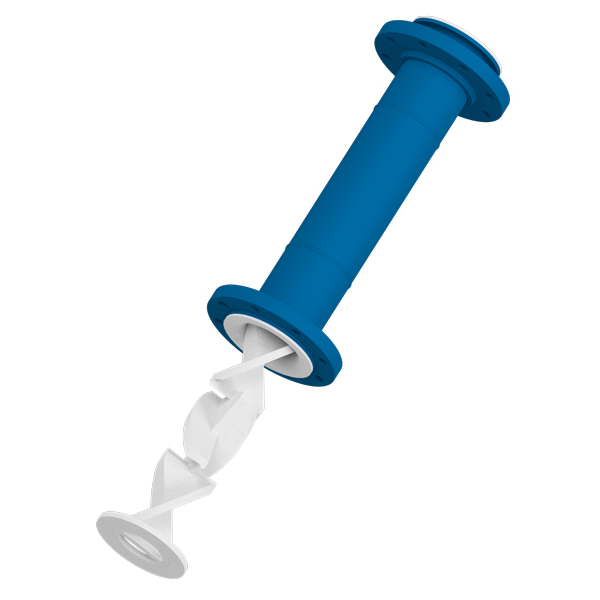
ELIGABLE FOR OUR QUICK SHIP PROGRAM
Need it quick? Quick Ship models ship within a few days!
How it Works
The Admixer CX static mixer and blender excels at processing any combination of miscible fluids. Where laminar flow exists, complete homogeneity is achieved through geometrically precise flow division regardless of viscosity, density or velocity. In turbulent flow, the Admixer CX utilizes radial momentum and inertia reversal to eliminate stratification of flow, temperature gradients and processed material variations.
For difficult mixing requirements involving immiscible fluids, gas and fluids, or other 2- and 3-phase operations, the Admixer CX static mixer approaches ideal plug flow combined with very uniform shear. This unique combination provides predictable droplet size formation and distribution for creating fine dispersions and stable emulsions. Where heating or cooling of fluids is critical, the Admixer CX will increase the heat transfer rate while eliminating temperature and velocity irregularities.
The Admixer CX static mixer geometry is computer-designed for optimal performance and reproducible manufacturing techniques. It will completely blend, disperse, react or heat two or more fluids in a short length of pipe. To achieve these results, the Admixer CX relies on the principles of radial momentum transfer, flow division and inertia reversal. These transport mechanisms eliminate concentration, velocity and thermal gradients.
While many geometric shapes have been used to create homogeneous flow, the degree of energy and mixing efficiency has been inadequately addressed. By using an elliptical or helical shape, smooth transitions are possible and no energy is wasted in back mixing. Triangular risers are used to connect the angled elliptical shapes to prevent eddy dissipation at the element edges.
When in laminar flow, two or more fluids will remain adjacent to each other indefinitely unless disrupted. The mixing elements divide the fluids and reorient by 180º, by reversing from left hand to right hand orientation, the rapid reversal at the interface enhances the mixing effect.
Model Specifications
Scroll to the right if needed to view all information.The following Technical Reports are available for understanding and applying the Admixer static technology.
Tech Notes
#101 – Admixer Theory of Operation
#102 – Sizing the Admixer
#105 – Gas Blending
Processing Reports
#201 – Sanitary Static Blending with the Admixer
Characteristics
Admixer CX Options
MATERIALS
- Teflon (PTFE) machined from solid bar
- Exotic alloys including Titanium, Monel, Hastelloy B & C, Carpenter-20 and others
MOUNTING
- Sanitary clamps
- Threaded ends
- Flanged ends
- Tri-clamp connections
OTHER
- Special surface finish and electropolish are available
- Retainer ring welded onto element for easy removability
- Welds can be completely ground, blended or polished
RELATED BLOG POSTS
Admix to Exhibit Full Mixer Portfolio at Process Expo 2019
Low Shear Mixer Portfolio
Admix to Showcase Robust Mixing Equipment Portfolio at Pack Expo International
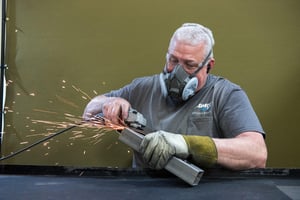